Maximising Space Without Moving Walls: How Smart Warehousing Solves the Land Cost Problem in Southeast Asia
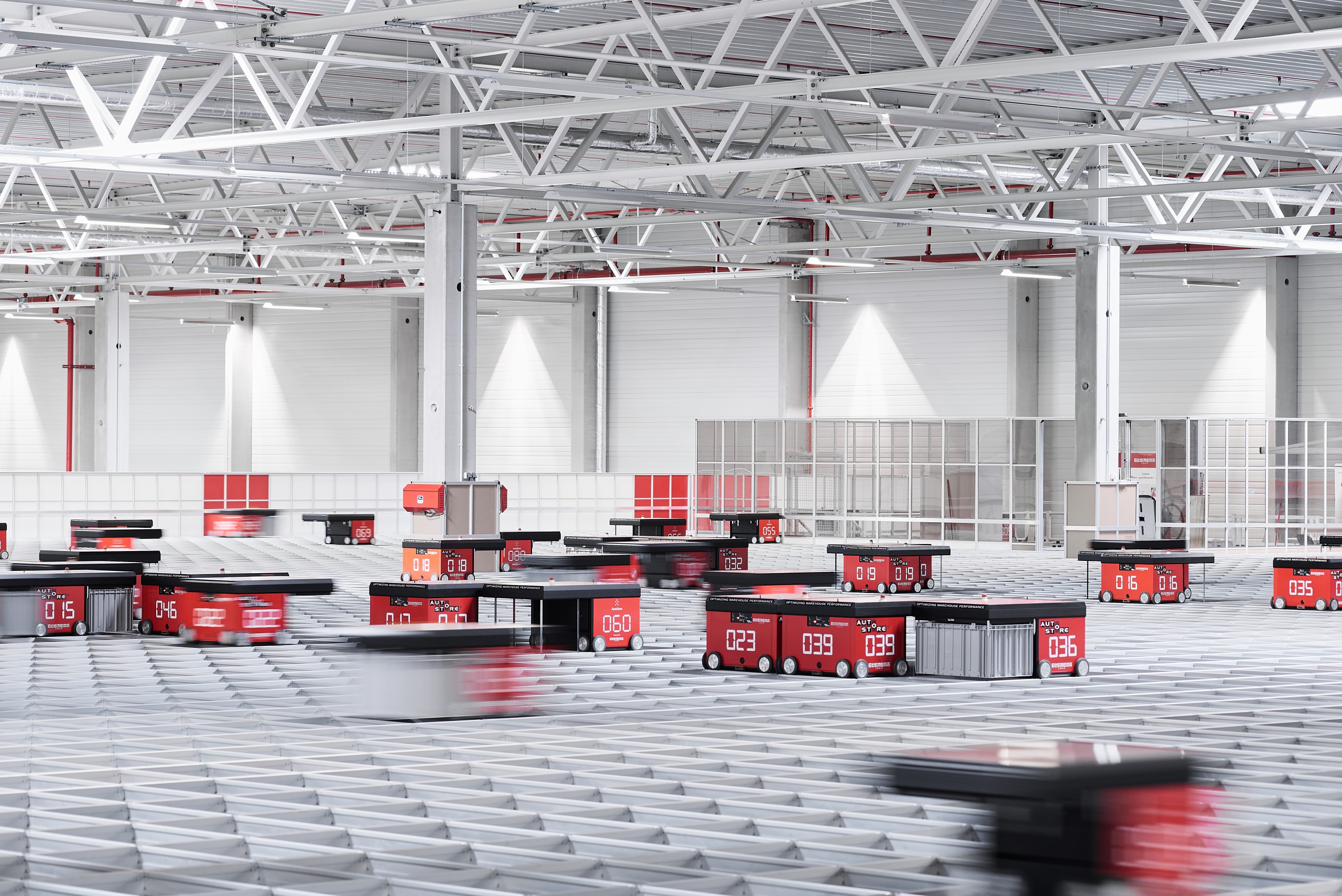
The Urban Logistics Squeeze: A Regional Challenge
In Southeast Asia’s rapidly urbanising cities like Singapore, Kuala Lumpur and Jakarta, the demand for warehouse space has surged, leading to escalating rental costs. For instance, in Singapore, warehouse rental prices range from $1.80 to $3.80 per square metre, reflecting the premium on industrial space in the city-state. Similarly, in Malaysia’s key areas like Klang Valley and Johor, rental costs can be as high as RM25 per square foot.
Traditional expansion methods, such as acquiring additional land or constructing new facilities, are often not viable due to limited availability and high costs. This scenario necessitates innovative solutions to optimise existing warehouse spaces without physical expansion.
The Hidden Cost of Inefficient Storage
Many warehouses in the region suffer from suboptimal space utilisation. Inefficient layouts, outdated racking systems, and reliance on manual processes contribute to underutilised vertical space and increased operational costs. According to industry insights, e-commerce enterprises typically require up to three times the capacity of traditional warehouse users to accommodate a higher range of items.
This inefficiency not only leads to higher storage costs but also affects order fulfilment speed and accuracy, impacting customer satisfaction and overall profitability.
Thinking Upwards: Smarter Systems for Leaner Floors
To address these challenges, businesses are turning to vertical storage and goods-to-person automation systems like AutoStore. AutoStore utilises a grid-based system where robots retrieve items from stacked bins, significantly increasing storage density. This system can store up to four times more inventory in the same footprint compared to traditional shelving.
By automating the storage and retrieval process, AutoStore not only maximises space utilisation but also enhances picking speed and accuracy, leading to improved operational efficiency and reduced labour costs.
From Floor Plan to Competitive Edge
Real-world implementations of AutoStore demonstrate its effectiveness. The Hut Group (THG), a UK-based e-commerce company, installed an AutoStore system with 300,000 bins and 256 robots, later expanding to 380 robots. This automation enabled THG to handle one million units daily and achieve a return on investment within 24 months.
Why It Matters More in Southeast Asia
Southeast Asia’s e-commerce sector is experiencing rapid growth, with revenue increasing by 28% year-on-year to $28 billion in 2023. This surge, driven by a rising middle class and increased internet penetration, intensifies the need for efficient warehousing solutions.
The region’s unique challenges—limited land availability, high rental costs, and growing demand for quick order fulfilment—make smart warehousing solutions like AutoStore particularly valuable. By optimising existing spaces, businesses can scale operations without the need for costly expansions.
Rethink Your Warehouse Before You Relocate
Before considering relocation or expansion, it’s crucial to assess the efficiency of your current warehouse space. Implementing smart warehousing solutions can unlock hidden potential within your existing facilities.
At Element Logic, we specialise in designing and implementing automated storage solutions tailored to your specific needs.