The essential guide to automated storage and retrieval systems (ASRS)
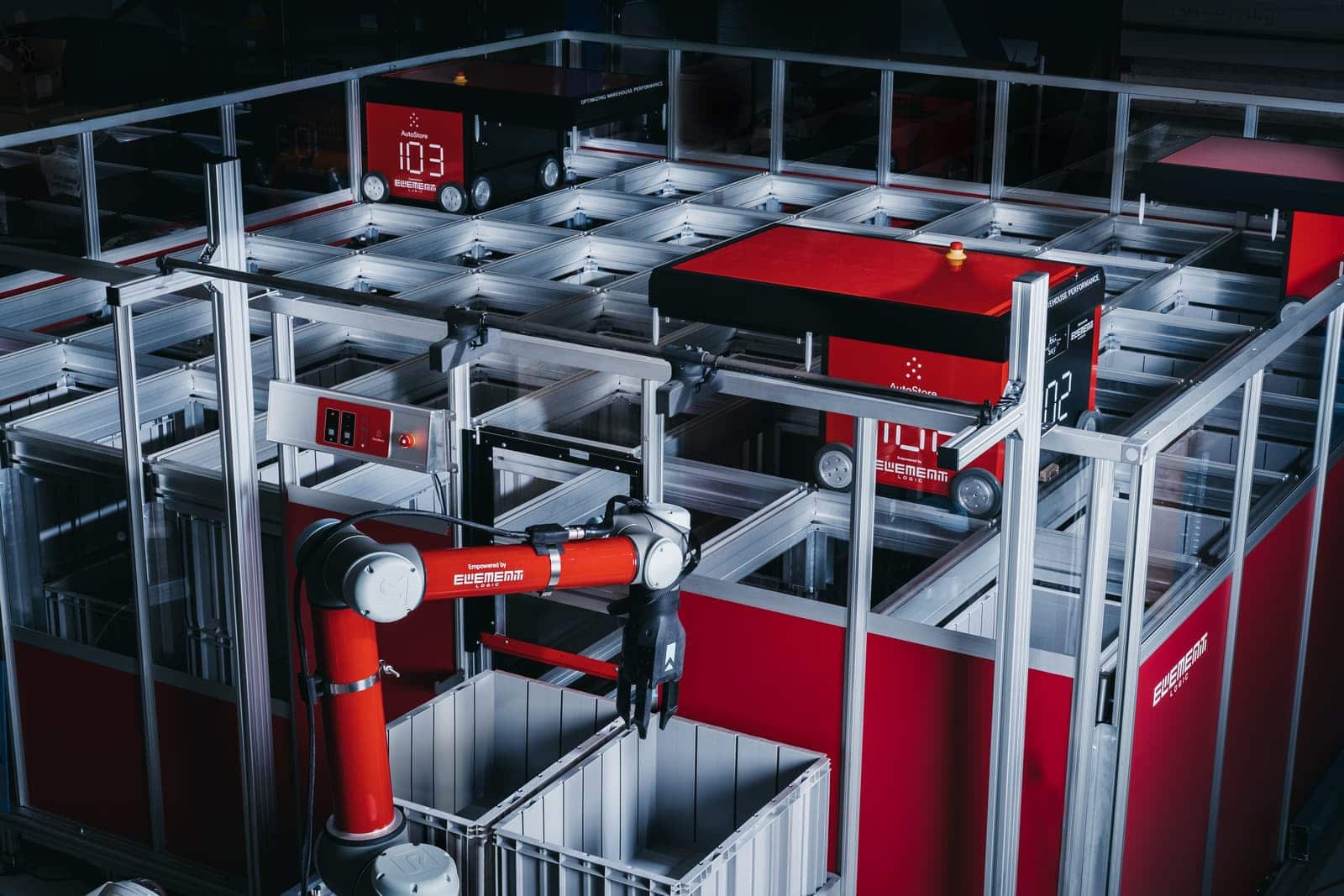
Digitalisation has completely changed the world of logistics. It’s now possible to purchase from different countries with ease as if they were “around the corner.” We live in a truly global market, and the need to stay ahead of the competition and grow in this ever changing landscape has driven companies to evaluate every aspect of their logistics operations.
This has increased the demand for automated systems and technologies to optimise the internal flow of materials, goods, and data within warehouses and distribution centres often referred to as intralogistics automation. From robotic picking and automated storage to AI driven warehouse management systems, intralogistics automation is redefining how modern operations move and manage inventory.
Among the most transformative technologies in this space are Automated Storage and Retrieval Systems (ASRS).
ASRS is reshaping warehouse logistics. Labour scarcity and the rising costs of recruitment and training show no signs of slowing, while property costs remain high and increasingly risky. ASRS can support the growing demands for efficiency and space optimisation. These computer controlled systems automate the handling, storage, and retrieval of goods to streamline operations while maximising capacity.
ASRS technologies vary significantly in complexity, from carousel based systems to sophisticated robotic cube based solutions like AutoStore. Understanding the strengths and limitations of each ASRS type is essential for making decisions that will enhance warehouse performance.
Equally important as the technology itself is choosing the right intralogistics partner. Design, implementation, and long term system support can dramatically influence the success of an ASRS project. In this regard, Element Logic stands out as the global market leader in ASRS design and installation, so we are well placed to help businesses transform a good automation project into a great one.
Breakdown of ASRS types
1. Carousel based ASRS
Carousel systems use rotating trays or bins, delivering items to a fixed workstation. Offered in both horizontal and vertical formats, they’re ideal for compact, repetitive pick tasks.
Advantages: Cost effective and space efficient for small parts and slow to medium moving SKUs.
Disadvantages: Limited to one pick location at a time; throughput is constrained and expansion requires additional machines.
2. Vertical lift module (VLM) ASRS
A VLM uses a central lift to access trays stored in columns, dynamically adjusting tray positions to maximise vertical space usage.
Advantages: Ideal for storing items of varying sizes, maximises vertical real estate, and offers good security.
Disadvantages: Sequential access limits retrieval speed; not optimal for high volume pick rates.
3. Mini load ASRS
Mini load systems use a crane mechanism to retrieve totes or trays from high density racking. Common in applications like store replenishment.
Advantages: Excellent for full case or tote picking and suited for predictable order profiles.
Disadvantages: Aisle bound cranes can be a single point of failure, and retrieval speed is limited by crane travel.
4. Robotic shuttle based ASRS
Shuttles move along tracks within racking systems to retrieve inventory. When paired with lifts and conveyors, they support multi level storage and high throughput.
Advantages: Fast and scalable, with high storage efficiency and multiple access points.
Disadvantages: High initial capital expenditure and relies on complex conveying infrastructure; not as adaptable to demand shifts without careful reconfiguration.
5. Robotic cube based ASRS (AutoStore)
AutoStore uses a grid of stacked bins and robots that travel over the grid to access inventory. It’s currently one of the most space-efficient and scalable ASRS solutions available.
Advantages: Offers up to 400% more storage in the same footprint, supports 24/7 operation, highly modular and energy efficient. Scales easily just add robots, ports, or bins. Easy to move to another facility if the operation and scope increases. Speed of build from order allows for systems to go live within a few months from purchase.
Disadvantages: The system is typically designed with a height limit of 16 bins (based on 330mm per bin). Mezzanine floors can be added if required to increase access levels.
6. Floor robots
While not ASRS by definition, floor robots such as AMRs (Autonomous Mobile Robots) can complement ASRS systems by transporting goods between zones.
Advantages: Quick to deploy, flexible, and ideal for brownfield installations.
Disadvantages: Lower storage density and payload capacity compared to fixed ASRS solutions.
AutoStore: A standout in robotic cube based ASRS
Among ASRS options, AutoStore represents the pinnacle of compact, high-throughput intralogistics automation. Its cube-based architecture stores inventory in a tightly packed grid, eliminating wasted air space. Autonomous robots move across the grid’s surface, retrieving bins and delivering them to operator ports with high precision and minimal energy use.
AutoStore is engineered to support operations with a high SKU variety, particularly in space limited environments where conventional storage solutions would be inefficient. Its modular configuration allows for seamless scalability, ensuring operations can expand incrementally without major infrastructure overhauls. Additionally, AutoStore’s low energy consumption and self-charging robots significantly reduce operational costs while enhancing order fulfilment speed and precision. With a range of robot models, workstations, and bin options, AutoStore offers a customisable system suited for businesses looking to balance dense storage with operational agility.
Element Logic is the world’s first and largest AutoStore integrator. With unmatched expertise, flexibility, and a proven track record, we help businesses unlock the full potential of their AutoStore investment. From system optimisation to future-ready scalability, we’re your partner in harnessing the latest advancements in warehouse automation. Our innovative products and tailored software solutions are purpose-built to maximise AutoStore performance and redefine traditional warehousing.
Conclusion
Intralogistics automation continues to evolve, and ASRS solutions are at the forefront of this transformation. For businesses facing increasing order volumes, labour challenges, and space constraints, an ASRS, particularly a solution like AutoStore, can deliver measurable gains in performance, efficiency, and long term cost savings.
However, no two warehouses are the same. Choosing the right ASRS technology and the right integration partner requires a clear understanding of your operational profile, future growth strategy, and flexibility needs. When deployed thoughtfully, intralogistics automation not only supports faster fulfilment but also creates a more resilient, scalable, and future proof supply chain.
For tailored ASRS guidance or to explore the potential of AutoStore in your facility, speak to our automation experts today and discover how Element Logic can help you lead the future of warehouse efficiency.