Element Logic Delivers its Most Advanced Warehouse Automation in Norway – for MEKO
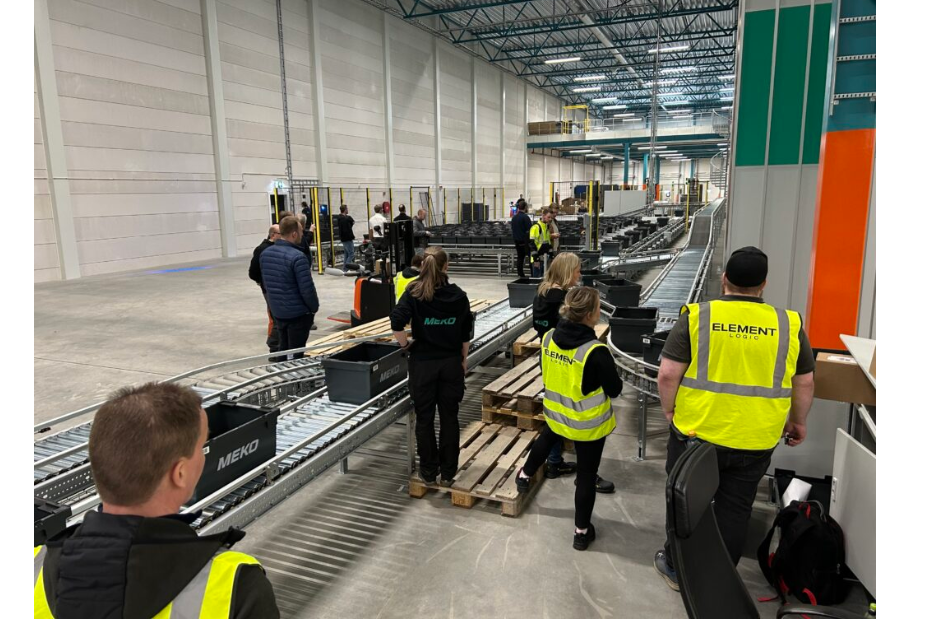
When MEKO consolidates its Norwegian logistics operations under one roof in Vestby, it is a direct response to a growing customer base, increasing demands for availability – and the need to make warehouse operations more sustainable and cost-efficient. The solution, designed and implemented in close collaboration with Element Logic, will be the most advanced automated warehouse facility Element Logic has delivered in Norway.
A Strategic Leap Towards the Future of Warehousing
MEKO is one of the leading Nordic companies within car parts, workshop equipment, and vehicle accessories. Until now, its logistics flows in Norway have been scattered and largely manual – with heavy reliance on the central warehouse in Strängnäs, Sweden. The new warehouse in Vestby, south of Oslo, represents a strategic investment in local presence, a wider assortment, increased capacity, and a future-proof approach to warehousing.
-We saw an opportunity to consolidate all our logistics flows in one location – while building efficiency and scalability into every aspect. From day one, we identified automation as a key component, says Tor Erik Myrvold, Logistics Manager for MEKO Norway.
![]()
We saw an opportunity to consolidate all our logistics flows in one location – while building efficiency and scalability into every aspect. From day one, we identified automation as a key component.
Tor Erik Myrvold, Logistics Manager for MEKO Norway.
AutoStore At the Center – and Much More
The heart of the warehouse is an AutoStore system from Element Logic, with 110,000 bins, 60 R5 robots, and 34 ports. The transaction capacity is impressive: up to 1,660 bin presentations per hour. But what really sets this facility apart is the complete solution.
-With this solution, MEKO has got a warehouse capable of handling significantly more orders, faster than before. We have simulated various flows and capacities to ensure the system meets both today’s needs and future growth. High transaction capacity means products reach customers faster – which is becoming increasingly important in an industry with high demands for speed and precision, says Niklas Poulsen, Account Manager Lead at Element Logic Norway.
![]()
With this solution, MEKO has got a warehouse capable of handling significantly more orders, faster than before. We have simulated various flows and capacities to ensure the system meets both today’s needs and future growth.
Niklas Poulsen, Account Manager Lead at Element Logic Norway.
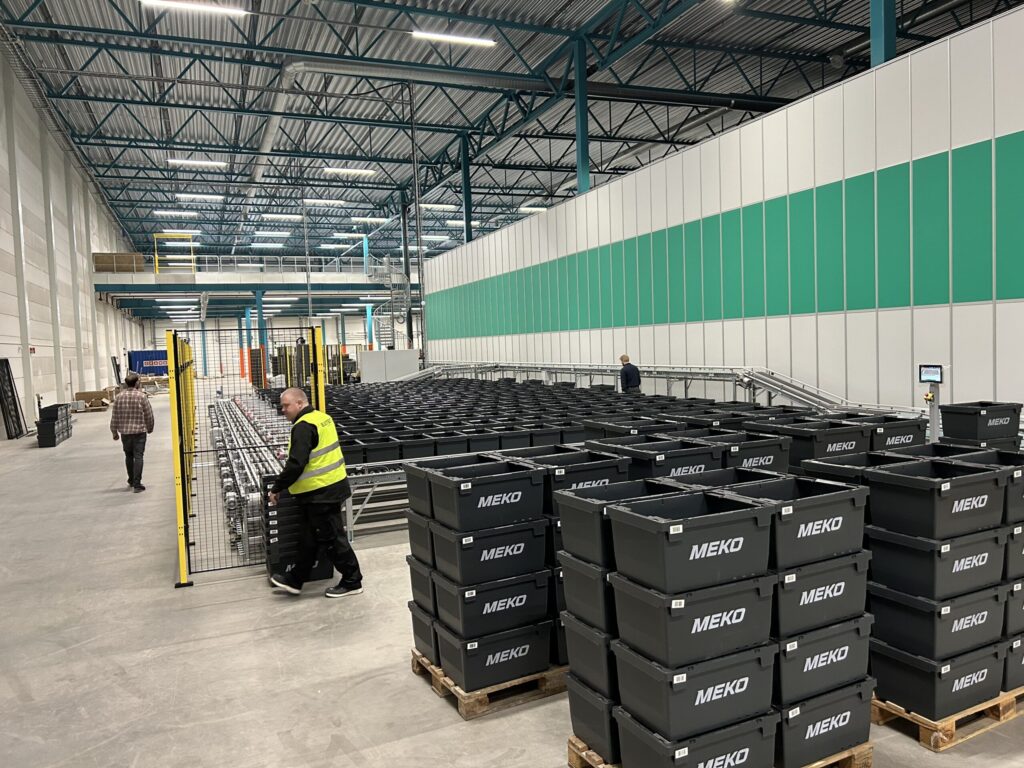
“The Most Advanced Facility We Have Built in Norway”
-AutoStore is just the beginning – the real uniqueness lies in how all the surrounding components work together: conveyor systems, robotic palletizing, put-to-light, buffer zones, sorting, and packing. This is the most advanced facility we have built in Norway – a clear example of how Element Logic develops complete, integrated warehouse solutions, says Tina Meffert, Project Manager at Element Logic Norway.
All components have been carefully coordinated and integrated by Element Logic – ensuring a seamless and efficient end-to-end solution.
Examples of integrated components:
- Automatic de-stacker and bin-lift for totes
- Palletizing robot and automatic stackers
- Y-cross and conveyor belts
- Buffer zones for destination sorting
- Sorting area and batch picking
- Put-to-light and pigeonhole system at ports
- Waste conveyor
![]()
AutoStore is just the beginning; the real uniqueness lies in how all the surrounding components work together: conveyor systems, robotic palletizing, put-to-light, buffer zones, sorting, and packing.
Tina Meffert, Project Manager at Element Logic Norway.
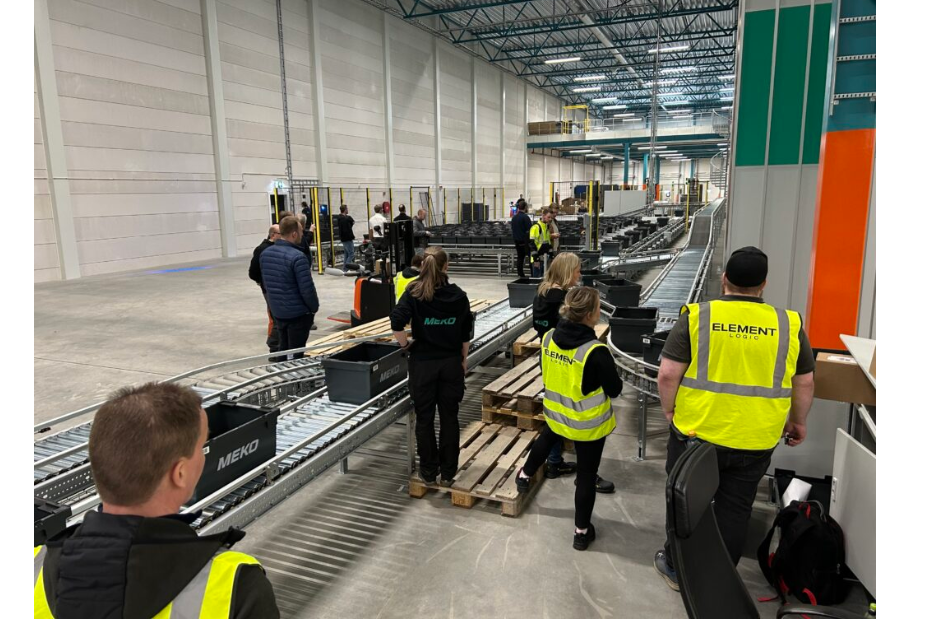
Built for Growth – and Real Sustainability
At 32,000 square meters, the warehouse is designed to grow alongside MEKO’s business. AutoStore currently occupies only around 10% of the floor space – yet handles the majority of all transactions. With a scalable system in place, expansion plans are already underway to accommodate future growth.
Sustainability has been a key focus throughout the project. The building is BREEAM-certified at the “Very Good” level, features rooftop solar panels, and includes energy-efficient solutions in everything from lighting to packaging and transportation.
From Vision to Reality
Go-live was scheduled for May 12, with the official opening on May 21. Full operations are expected by July 1. But this is more than just a new logistics facility – it represents a new way of working.
-This project is about setting a new standard for MEKO’s quality and service – where customers will notice the difference – in delivery precision, product availability, and assortment,” concludes Tina Meffert from Element Logic.
![]()
This project is about setting a new standard for MEKO’s quality and service – where customers will notice the difference – in delivery precision, product availability, and assortment.
Tina Meffert, Project Manager at Element Logic Norway.
Interview with Tor Erik Myrvold, Logistics Manager, MEKO Norway
Why did you decide to build an entirely new central warehouse in Norway?
-We have lacked a central logistics hub in Norway. Previously, we operated several smaller warehouses alongside the central warehouse in Strängnäs, which made it difficult to work as efficiently as we wanted. Now, we are consolidating everything under one roof and gaining full control of the entire supply chain – while also getting closer to our Norwegian customers.
Why was automation the obvious choice?
-Our previous setup was entirely manual, which was both labor-intensive and inefficient long-term. Plus, our most frequently picked products are ideally suited for automated handling. It is about future-proofing the business – but also about creating a better working environment, higher quality, and improved profitability.
Why did you choose Element Logic as your partner?
-When evaluating different suppliers, it became clear that Element Logic could deliver a complete solution. They have extensive expertise in AutoStore and, throughout this project, have also significantly developed their capabilities within conveyor systems and other automation technologies. Element Logic has been incredibly flexible – we even relocated the entire project site, and they adapted the design accordingly.
How will this impact your customers?
-Customers will notice the difference. Faster deliveries, greater product availability, and a wider assortment thanks to improved space efficiency. We are also increasing delivery quality, which was already at a high level, by automating more parts of the operation.
Has the project led to any changes for employees?
-Absolutely. Employees from both MEKO and our sister company Sørensen & Balchen will work here, and they will be trained on the new system. Element Logic has developed a training program to ensure a smooth transition to the new technology.
Are there already plans for future expansion?
-Yes, we have designed the warehouse to allow expansion in several directions. The AutoStore system is scalable, and we already have concrete plans to expand as demand grows. We see this as a long-term solution we can grow with.
What does this investment mean for MEKO in Norway long-term?
-It is a key milestone. With greater efficiency, improved precision, and increased flexibility, we can strengthen our market position. We are bringing our entire operation under one roof – building a robust logistics hub for the future.
Facts and Figures:
- 110,000 bins (with capacity for 120,000)
- 60 R5 robots
- 34 ports
- 1,660 bin presentations per hour (transaction capacity)
- Software: eController, eHub, eManager
- 15,000 internal bins
- Waste conveyor
- Automated tote feeding with de-stackers
- Complete takeaway conveyor from ports to sorter
- Buffer solution and automated tote palletizing