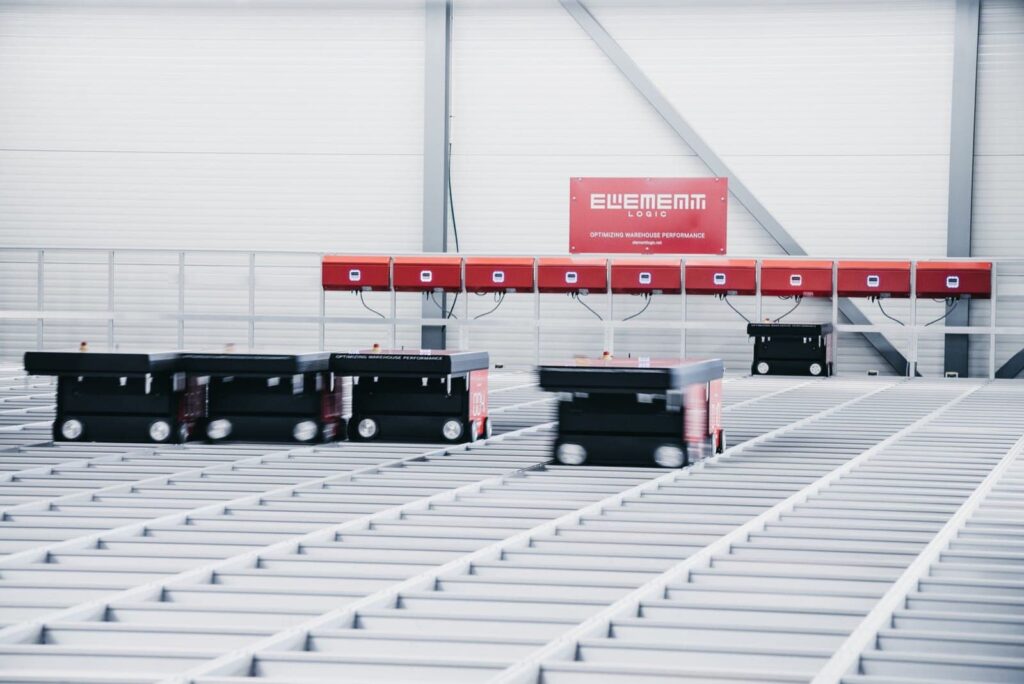
FAQ
Common questions about AutoStore
System
Each AutoStore module is approved for a temperature range of 2-35 degrees Celsius (35-95 degrees F). A system operation temperature of 18-25 degrees can be considered as normal. Operating Humidity on the modules is 40-90%, NON-CONDENSING.
Element Logic can integrate your AutoStore system with existing software.
Element Logic delivers complete projects including design, software, installation, implementation, documentation and customer care.
Yes, all activity among other failures are logged and are traceable. The EWMS can trace all bins via Log Publisher. The Customer/EWMS needs to maintain the bin contents and needs to back-up all critical data.
Yes. Ports are equipped with security measures to ensure workers are not injured during operation.
Example: An installation with 16 bins in height and 30kg (66lbs) load = 2000kg/sqm. If you are uncertain, please contact our team for further assistance.
AutoStore standard is a max weight of 30kg/bin (66lbs/bin). Further development is “demand-and-market-driven”.
This will really vary case-by-case since there are many issues influencing this such as picking speed before and after, error reduction ratio, and storage area reduction.
Yes, our only requirement is that the top of (each) grid is flat (on the same height level).
Yes. Bins can be exchanged between the different floor levels via connecting bin lifts.
No, with an AutoStore installation you may surround obstacles like pillars, pipes and walls.
705mm (27.75in) in wide grid and 480mm (18.9in) in narrow grid direction.
It is possible to use AutoStore modules in a refrigerated warehouse down to 2 degrees Celsius (35 degrees F) under the circumstances that you have a constant environment (e.g. low, constant humidity and temperature). Even though the modules will work in this environment, we have not realized any installation in chilled environment yet. Operating Humidity on the modules is 40-90%, NON-CONDENSING.
No, currently it is not approved by AutoStore to use an AutoStore installation in environments with less than 2 degrees Celsius (35 degrees F). A separate development of an “AutoStore freeze” is not planned at the moment.
Yes, there are some requirements in accordance with industrial standards listed in our AutoStore pre-installation manual. If you are uncertain, please contact us for further assistance.
Yes, the system was, in fact, designed for usage in the electronic component business in its origin. The AutoStore bins exist also in a PP-ESD variant.
The modules only have IP20 and are not approved for clean room environment.
Normal orders should be known some time in advance (30 min) to be able to dig up the bins to a higher level and give a more stable throughput. More urgent orders are also possible, but it might require some extra free robot capacity. To dig up a bin from the lower level of the grid (level 16), it normally takes about 3.36 min. Transportation time to the port is not included. (In a worst case situation, dig-up might take 5-10 minutes due to temporary blocking of the area by another dig-up job).
AutoStore is operating with >=98% system availability. Statistics from AutoStore’s 100+ installations show >99.6% availability in average. For an AutoStore installation with 50 robots and 12-16 hour shifts, it is expected a failure rate of 2-3 short stops per working day. Typically, a stop could implicate a fast stop/start procedure of the system and last for approximately 3 minutes. But it is important to know that in most of the possible failure situations only parts of the entire system will go down. AutoStore will handle them automatically or they can be handled locally at the workstations.
Typically, a stop could implicate a fast stop/start procedure of the system and last for approximately 3 minutes. It is important to know that in most of the normal possible failure situations only parts of the entire system will go down.
Night preparation is a strategy where the Customer knows all or maybe only a certain number of bins needed to fulfill the orders the next day. The orders are already in the system the evening before and the Customer could benefit from pre-digging them up at night. The more bins known the better the night preparation and the new bin distribution will be. It is possible as long as the robots get enough charging during the night. It might be necessary to have a super user on site if something goes wrong during the night.
Forecast is a strategy used by the Customer to predict the usage of bins for the next day based on data from the past (statistically from previous days or years). The idea is to prepare a certain number of SKUs (bins) at night so when the picking activity starts the next day, we can get a good match between the real orders and these forecasted bins. Only with a very high hit rate of the forecast will be the usage of the forecasting strategy beneficial.
Best in class.
AutoStore use 10-15% of energy, compared with miniload.
Yes, it is possible to extend the installation during “normal” operation. Add robots and ports – during operation Add grid cells – parts of the grid can still be used while extending the grid.
You only need to have a AutoStore trained super user on site. (will usually work beside AutoStore with other tasks too e.g. picking shift leader).
AutoStore have performed extensive earthquake tests of the system in both Japan and the US. There is no general approval/test/certificate; Element Logic can take care of the local requirements.
We continuously work to improve the performance of the AutoStore system, both on hardware and software.
A bin lift can connect two AutoStore grids to each other. It will be two separate systems, with two controllers/Planners/SQL Database. A new module, G2GPortManager, will keep contact between both Controllers, listen to both ASlog files, and send messages to both systems. If one bin leaves one grid via the bin lift it will be removed from the originating grid’s database. When it enters the second grid via the bin lift, it will be inserted to the database of the second grid. The WMS needs to maintain and balance the bin level in both installations.
No, but there are several solutions to protect AutoStore (e.g. sprinkler). More and more customers also use an oxygen reduction process. The design recommendations for automated sprinkler systems are based on standards such as FM Global Data Sheets 8-9, NFPA13, EN12845 or VdS CEA 4001.
The chances for a fire starting and developing within a AutoStore system are limited. This is due to the way we stack the Bins on top of each other combined with the unique bin design. AutoStore is carefully designed and has specifically tested for fires over the last 10 years.
AutoStore is continuously running validated fire tests with institutions worldwide and have done so during the last 10 years. Based on this experience there is a fire protection manual available. Contact Element Logic for more information.
Yes, AutoStore has done many fire-tests over the last 10 years, and are continuously making improvements to reduce risks in general.
Bins
Max load today = 30 kg (66 lbs)
We have both types: PP ESD (black) and the standard not anti-static HDPE (grey).
Yes. You may split a bin in several compartments. AutoStore bins are also prepared for the usage of physical dividers. It is up to the EWMS to administrate and maintain the content of the bins (stock/SKU).
No, this could cause errors in the system. A bin with overweight will not be accepted at the AutoStore ports (overweight control).
It is possible to take bins out of the system at “transfer” ports, but the bins need to be handled in a controlled, closed environment (e.g. a conveyor loop) to reduce risks for bin damages.
Inside dimensions: 600x400xx310mm (330mm Bin) 600x400x200mm (220mm Bin)
It is not an official AutoStore module at present, but bin with a lid is under developement.
Dimensioning
Max height of grid: Please see question below Max load per bin: 30 kg (66 lbs) We consider installations with a size of: – cells in X/Y >255 (~1,000,000 330mm bins) – more than 254 robots as special installations. We have technical solutions to realize even bigger installations, but from operational point of view is it recommended to split such big installations into several smaller once (mainly due to throughput impact of a stop situation).
The max height is a stack of 16 of 330mm bins or 24 of the 220mm bins resulting in a height of about 5.4m (17.75 feet). Robots and recommended service increase the height to 7.4m (24.25 feet) in total Design guidelines: 1. A grid width/length ratio in meters between 1:1 and 1:3 is preferable. 2. Minimum grid size (width/length) in number of cells is the number of bins in height plus 2 in each direction. 3. To prevent robot “over-population” there should be at least 15-25 grid cells per robot (rule of thumb is 25). 4. If the conditions are not as specified in points 1-3, an AutoStore installation can be still a very efficient solution, but a specific analysis/simulation is recommended.
1 bin plus a track above it. Or even less if the track is used “only” as a road for transporting bins between different grids. If only the tracks or 1-bin is defined, the system still needs to be secured by a supporting structure.
For robot trafficking we need at least 600mm (2 feet). Space for service and support staff to operate and use the AutoStore service vehicle on the grid should also be considered. AutoStore’s recommendation is at least 2m (6.5 feet) free height above the grid. In special cases a lower height could be accepted by the local authorities, but this need to be clarified and approved by the local authorities and Element Logic.
3mm (0.12 inch) on all sides (bin tolerance +/- 2mm)
Yes.
(Theoretical technical max port speed in bin presentations per hour) For Conveyor ports: -At mezzanine level: Up to 240 exchanges/hour (4 exchange/min) -At ground floor level: Up to 180 exchanges/hour (3 exchange/min) Minimum exchange time: 5 seconds, 1 second for weight control, and 1 second for NSH For carousel ports: -At mezzanine level: Up to 500 exchanges/hour (8 exchange/min) -At ground floor level: Up to 400 exchanges/hour (6 exchange/min) Minimum exchange time: 3 seconds For Swing ports: -At 8m: Up to 160 bins/hour -At 12m: Up to 140 bins/hour -At 16m: Up to 125 bins/hour Minimum exchange time: 3 seconds Different from case-to-case. Fastest installation today: Carousel: ~ 360 Conveyor: (200-240) A higher throughput per workstation can be achieved by: – batching / grouping of bins (one bin presentation per x picks) – having several ports per workstation
Yes, there are a couple of ways this could be achieved. 1. AutoStore always counts the real bin deliveries, but quite often a customer can reach extra pick capacity by using the “batch” effect (i.e. the operator consolidates at one port several orders at the same time). These orders are selected by the WMS to reach the best fit of SKU request (i.e. from one delivered bin/SKU can the operator pick to several orders). 2. Several AutoStore ports can be grouped close together to create a work station served by one and the same operator. Compared to a single port work station the operator can achieve a much higher efficiency. 3. A combination out of point 1 and 2.
Ports
Yes, changes of already a transferred task or task groups to AutoStore are possible, but each change later on may have negative influence on the speed and efficiency of the system as the system may already have used robot resources to prepare that bin.
We offer a WSH Swing port only.
The lift module can be delivered in 5.5m (18 feet), 11m (36 feet), or 16.5m (54 feet) and adjusted on site to the correct height.
Speed is 2,5m/second. Acceleration is 2,5m/second2.
Swing ports need at least two (2) cells between each other, both in the x- and y- direction. When they are placed 2 cells apart in the x direction they must be facing opposite directions to leave space for the picker.
As with each AutoStore port, each swing port has its own port firmware.
This is not an available solution today. It is based on real case requests and can take some time (12 months+) for development after an order is placed with AutoStore.
Robots
2.4GHz is used globally.
2.4 GHz: Up to 30 robots (Max 50)/ std. range circle 25m radius per AP (max up to 50m). Old installations in Europe: 433MHZ: Up to 30robots / std. range circle 25m radius per AP (max up to 50m). Old installations in US: 915MHz: Up to 30 robots (Max 50)/ std. range circle 25m radius per AP (max up to 50m).
This need is decided case-by-case. A minimum setup for each installation is 2AP. In special cases you will need extra AP to avoid black spots due to building constructions.
Currently the standard is one charging point per robot. We test with a ratio of 70% chargers per robot for the moment. Further development is ongoing to change this ratio to 1:2 or even less in special cases.
R5: Max speed = 3,1 m/second (10 feet/second); Acceleration = 0,8 m/second2 (2.6 feet/second); Lifting speed = 1,6 m/second (5.25 feet/second) B1: Max speed = 4 m/second (13 feet/second); Acceleration = 1,4 m/second2 (4.6 feet/second); Lifting speed = 1,6 m/second (5.25 feet/second)
This is hard coded and controlled in robot firmware.
Example of 16 bin levels: Minimum 3 minutes 36 seconds (plus 3:36 for cleaning up afterwards). But this digging process will normally be done in background and in advance of a bin request and presentation at a port.
No. In the most situations the system will continue running. The AutoStore software module XHandler is taking over the failed robot and will try to fix the error situation without stopping the system. Only in situations that cannot be handled automatically or there is a risk of robot collision will the system stop.
The ACS software plans and controls the robot traffic to ensure robots do not collide. The robot reports its position continuously to the ACS software. The robot driving control is done by the motor encoder and secured by two different track sensors for each direction.
Estimated lifetime for the Chairman AGM 12105T battery used in AutoStore R5: – System runs 8 hours a day, 5 days a week: 8 years – System runs 16 hours a day, 5 days a week: 4 years – System runs more than 16 hours a day, more than 5 days a week: 2 – 4 years.
R5: The robot weight including batteries is 148 kg (326.28 lbs). With maximum loaded bin, this would be 148 kg +30 kg + ~5 = ~183 Kilo (326.28 lbs + 66 lbs + ~11 = 403.44 lbs)
R5 uses 12V/105Ah AGM batteries (lead acid – Absorbed Glass Mat) as a standard.
This is really case orientated. A rough rule of thumb is 25 bin presentations per robot per hour +/-. But even up to 40 bins/robot is possible. Simulation can test this.
Normal working day for R5 is about 20 hours. Each robot need at least 4 hours continuously charging per day. With a constant performance claim during the day with more than 8-10 hours operation: the robots need to have the possibility to get short high-speed charging periods during the working day e.g. during break or low capacity periods, or extra robots is needed. For 24 hour operation: A certain number of extra robots is needed to realize the charging needs and secure a long battery life time.
Yes.
Yes, but extremely unbalanced load (e.g. 30kg/66lbs in one corner or less than 1/3 of the compartment) can increase abrasion of wear parts.
This is dependent on weight, driving frequency, lifting frequency, operation hours, etc.
Product Safety
The primary area of focus of AutoStore is safety. In particular, fire safety is of paramount importance. It is not enough to develop ways to extinguish a fire once it has started. Of far greater significance are the measures and methods employed to prevent fire from starting in the first place.
All AutoStore products are tested and approved by external and independent agencies with long track records in their respective fields of expertise. As of today, AutoStore has an approval process covering various aspects of its product range in 19 different areas.
For the European market, there are many directives such as LVD, EMC, RED, and the EU Machinery Directive. These are an integral part of the safety-approval process and are also grouped together under the auspices of CE certification. CE marking, as it is known, is a system that relies upon self-declaration. For AutoStore, it is imperative that all our product approvals are tested, approved, and certified by accredited agencies such as those described above. On a similar footing in other regions of the world, AutoStore relies on certification from accredited bodies able to carry out the necessary safety tests of their products. This lets us maintain the high level of quality we require and which our customers expect.
Prevention is the best policy
Since 2009 AutoStore has performed on-going tests of the entire system, in both Europe and the USA, for fire safety. These tests include various sprinkler configurations, height ratios in relation to overhanging ceilings, and compact storage-unit density. Observations have revealed that even with a high-density storage of combustible materials present in the storage facility, fire growth has been retarded due to the lack of available or circulating oxygen otherwise necessary for a fire to expand and intensify.
In terms of AutoStore modules, tests on the various products have been extensive, all of which have resulted in a voluminous portfolio of reports and certificates. Some of the most relevant approval tests are listed below.
LVD – Low Voltage Directive:
This test exposes the modules to fabricated faults and stresses with the intention of ensuring that heat does not form thus becoming a fire source or creating a risk to personnel.
EMC – Electromagnetic Compatible Directive:
This test is performed to ensure that the modules do not adversely affect other machines and also that AutoStore modules are not affected by electromagnetic radiation. This extensive examination includes testing for antistatic interference.
EU Machinery Directive:
This directive shall ensure that a machine is safe to use and that it does not represent a risk of physical injury to users.
RED – Radio Equipment Directive:
As some of the products contain radio transceivers, it is extremely important that we do not breach legally established frequency wavelengths. This encompasses transmitter power and the frequency range the products transmit on.
ETL – Electrical Testing Laboratory:
The ETL Mark is recognized as proof that a product follows North American safety standards. Authorities and code officials across the US and Canada accept the ETL Listed Mark as proof of product compliance with established industry standards. The mark is accepted by retail buyers on products being sourced, while for consumers it is readily recognizable on multiple products as a symbol of safety.