Aiming for speedy delivery with a new warehouse system
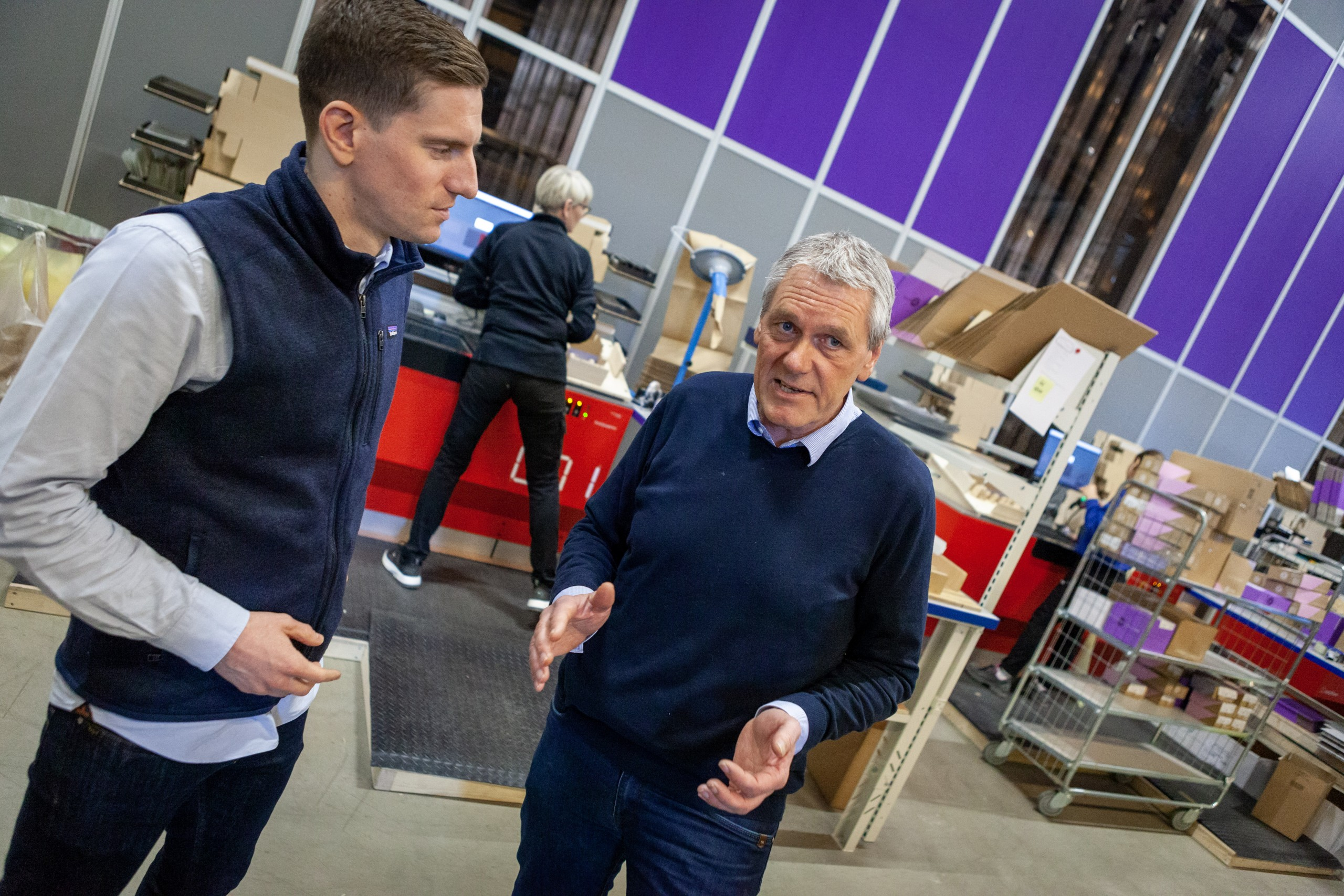
“At some point, efficiency figures reach a peak with manual storage. We have countered that by implementing AutoStore”.
Vidar Solberg, Head of Logistics at the cosmetic and hygiene company VITA, is enthusiastic about his warehouse in Mjøndalen. In the background, the AutoStore system implemented by Element Logic is fully operational.
“Two years ago, we started the process of researching what to do when the lease expired in 2022. We carried out an extensive study which resulted in an extension of the lease agreement, while also deciding to opt for a custom-made AutoStore solution. It’s a choice we feel very confident about,” Solberg says.

Significant online growth
Alongside the existing warehouse of 3,200 m2, VITA expanded with a hall of 500 m2. This is where the new robotic system for order picking is located.
“We have three streams of goods at our location today. One is supplying to the store, which occurs in a pure throughput warehouse – the goods are not even touching the shelves. VITA also has several of its own brands, that we stock from other parts of Europe. In this area, we operate as a regular wholesale warehouse. Then there is the third stream of goods which is out to the consumer – now being served by the automated solution,” says Solberg.
Approximately 12,000 product lines are placed in the AutoStore, which is equipped with 17 robots and five ports. A central driving force for the investment is VITA’s significant online growth over recent years. Both in terms of the number of orders and number of items. And as a symptom, longer picking routes.
“We reached the limit of what we could achieve in the manual warehouse, and we saw a risk that key figures would start to decrease if we continued with a manual warehouse. With AutoStore in place, we have a goal of 120 product lines per hour per employee, when picking items for online orders. And we aim for a turnover this year of just over 160 million in the online store. We are on track to achieve that,” says Solberg.
![]()
With the choice we made, we now have full control of our logistics – which is important to us.
Vidar Solberg, Head of Logistics at VITA
Fast delivery as mantra
One of VITA’s mantras is speedy delivery.
“We have many competitors both domestically and abroad, and relying solely on the lowest price will not be sustainable over time. So, for us, one of the competitive advantages is quick delivery to the customer,” says Solberg.
He adds that they are now well-equipped to take new steps in the coming years.
“Today we have 10,000 bins, but the system is scalable. After we built the new hall, we have the capacity to expand with an additional 21,000 bins without having to build larger.
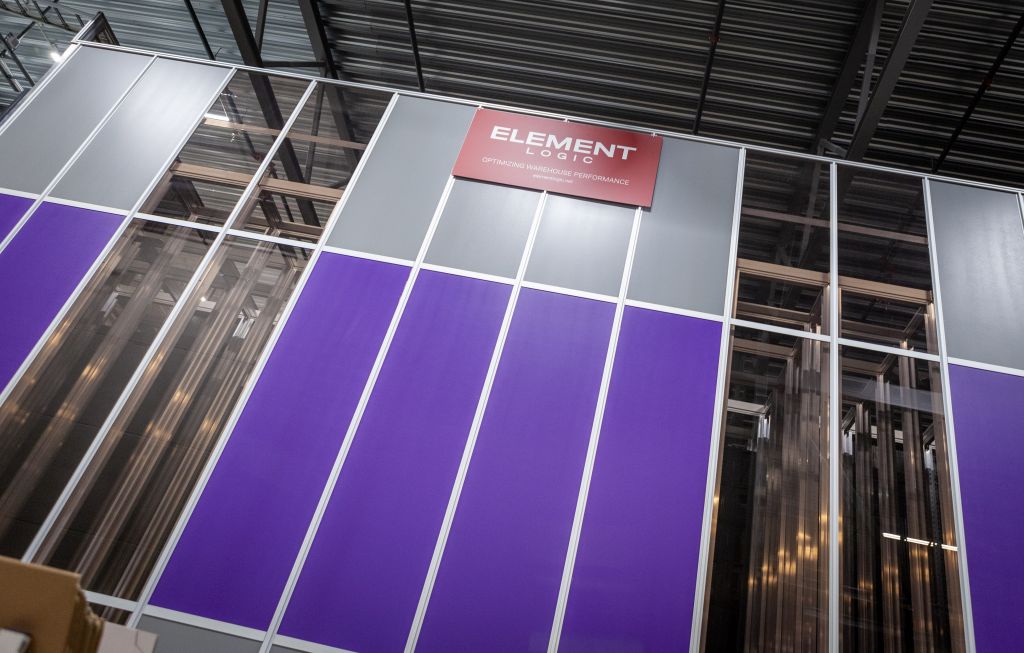
Full control
Solberg is clear, that VITA, with a total of 116 stores, did not only consider the AutoStore benefits when they faced the manual warehouse limitations a while back.
“Many options were considered. We had concrete offers from 3PL providers, but we believed we could do it cheaper ourselves. And with the choice we made, we have full control of logistics – which is important to us,” says Solberg.
He is joined by colleague Kristian Sonnenberg, Chief of Technology and Digitalization (CTO) at VITA.
“Based on the customer’s expectation of a seamless shopping experience across web and physical stores, we saw that we had to make a major change to the entire software portfolio. The AutoStore solution is part of a digital strategy for VITA where we are changing all core systems and moving much of the portfolio to the cloud,” says Sonnenberg.
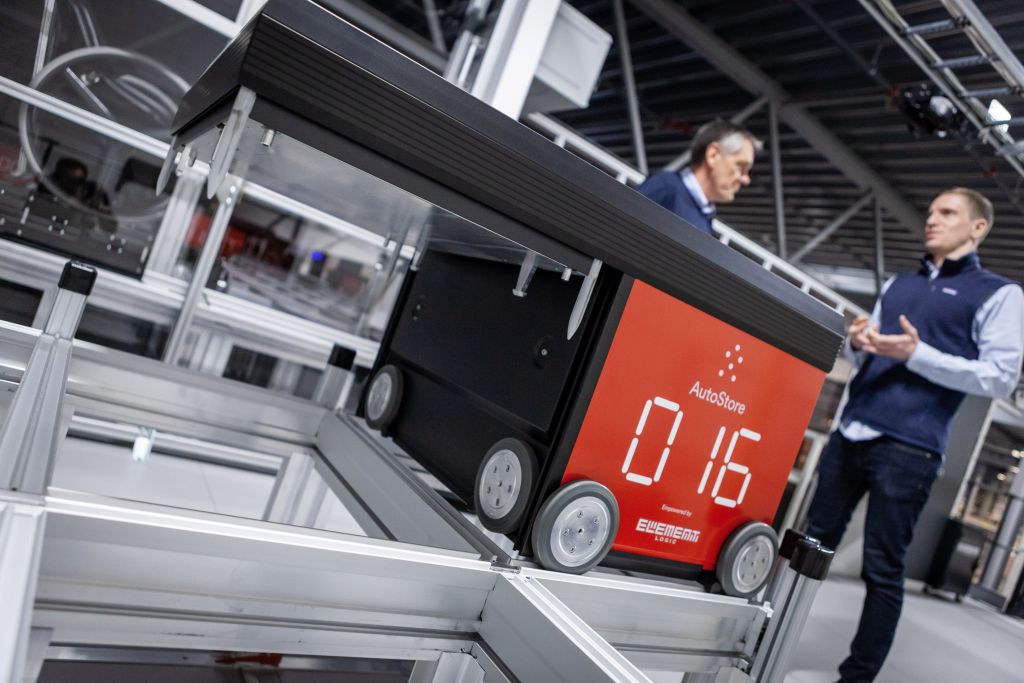
Solid partner
The VITA team clearly states that the cooperation with Element Logic has met the high expectations.
“They have had complete control from A to Z. The process has been very predictable, both in terms of timelines and costs. At the slightest increase in risk, they were there immediately. It has felt very safe to work with them,” says Sonnenberg, and is supplemented by Solberg.
“The project execution from Element Logic’s side has been a top-notch experience. They have been incredibly easy to work with,” he believes.
It is still too early to determine what will be the long-term result for VITA with the commitment to the automated warehouse system. However, they have already started to see the effect.
“We need to wait a few months for statistics, but we already see the positive trend. There’s no doubt about it,” concludes Vidar Solberg.
VITA facts and figures:
- 3,700 m2 warehouse
- 10,000 bins (capacity for 31,000)
- 12,000 product lines in AutoStore
- 17 robots
- Five ports